The Replenishment Handbook
A Comprehensive ML-Powered Replenishment Guide to Unlock Greater Cost Savings and Customer Satisfaction with Optimal Inventory
Table of contents
- Understanding Inventory Replenishment
- Why Does Intelligent Replenishment Matter?
- What Impacts Inventory Replenishment: External & Internal Factors
- Optimizing Inventory Replenishment
- Benefits of Replenishment Optimization
- Challenges in Inventory Optimization
- Optimizing Inventory With Intelligent Automation
- Intelligent Inventory Optimization Strategies to Reduce Costs and Improve CX
- How Can Algonomy Help?
As many as 65% of organizations focus on optimizing inventory to reduce their overall supply chain costs. Yet, a whopping 55% of them struggle when it comes to forecast accuracy, inventory placement, and order fulfillment. Inefficiencies in inventory management are more than mere operational hurdles and stem from a nexus of multiple issues at multiple levels in supply chains.
The inability to sync inventory with demand ties up crucial capital in excessive stock, disrupts the entire network, and ultimately leads to the loss of customer trust due to inadequate availability.
Market studies reveal that 68% of organizations face difficulties in demand planning owing to the lack of data on fluctuating demand, and 74% of them face shipment delays or longer lead times owing to inefficient inventory management.
Then, what is the best way to optimize inventory, and how can businesses target replenishment as a single function of all variables, such as operational costs, customer satisfaction, and demand planning? What role does accurate forecasting play in achieving optimal inventory, and why do businesses need to focus on the end-to-end picture for the best results?
In the following guide, we explore the answers to these and many other questions, talk about inventory replenishment at length, and share intelligent inventory optimization strategies to reduce costs and boost customer satisfaction.
Understanding Inventory Replenishment
Inventory replenishment or stock replenishment means restocking inventory in a warehouse or store such that the consumer demand is met optimally without overstock or out-of-stock events. While overstocking ties up the working capital, out-of-stock instances directly impact sales and customer experience.
Stats reveal that at least 74% of businesses experience delays in shipments, causing longer lead times. Further, retailers in the US alone lost a staggering USD 82 billion because of out-of-stock items.
Optimal replenishment ensures that the store/product location has sufficient stock without ballooning the inventory costs.
Replenishment Planning
It is a systematic approach to inventory management that ensures optimal stock levels are always maintained to meet customer demand without overstocking.
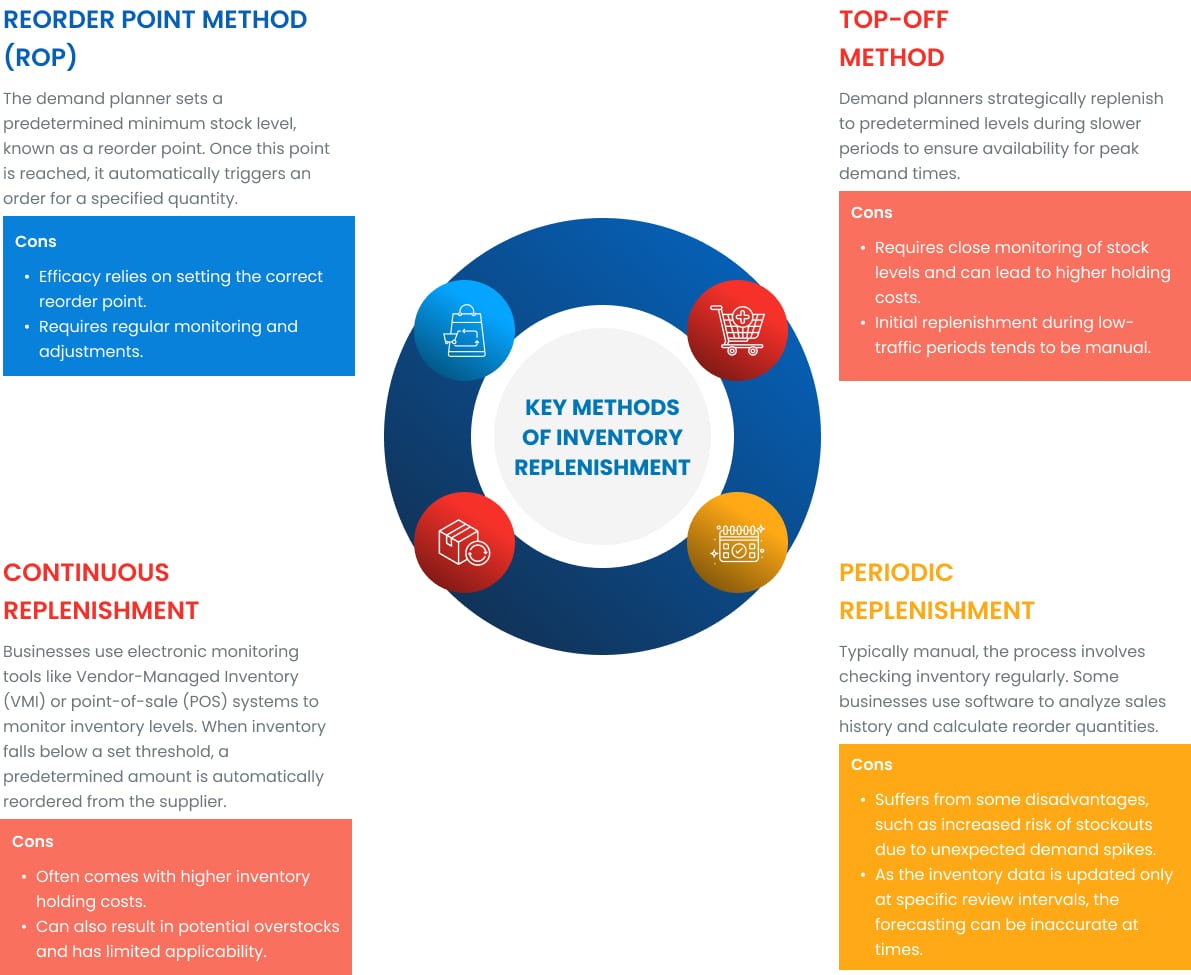
Three core functions of replenishment planning are – predicting demand/demand planning, configuring reorder points, and setting optimal reorder quantities.
Demand Forecasting
Demand forecasting as a function predicts future demand for specific products by analyzing historical sales data, seasonal trends, promotional activities, and more, to decide the right amount of inventory at a given time.
Ensuring high accuracy in demand forecasting has a direct impact on the overall replenishment efficiency as it helps businesses avoid overstock (resulting in increased carrying costs), and understock (leading to lost sales).
As per McKinsey, AI-powered forecasting can reduce supply chain errors by 20-50% and lost sales & product unavailability by up to 65%. It can also reduce warehouse costs by 5-10% and administration costs by 25-40%.
Inventory Management
Managing inventory involves three core tasks:
- Tracking the current levels of inventory across all product locations, such as warehouses, stores, etc.
- Monitoring stock levels for each SKU/product while accounting for lead times.
- Managing safety stock levels (buffer stock) to mitigate unexpected demand spikes and lows.
Order Fulfillment
This involves finding out the most efficient way to replenish inventory and involves activities like – ordering the right quantity of the right products while factoring in variables like lead times, demand, and storage costs.
Apart from ordering the right quantities, businesses have to ensure an appropriate ordering frequency as per demand patterns, lead times, etc. Identifying the most cost-effective supplier or warehouse location for optimizing inventory sourcing costs, and optimizing delivery schedules to curb transportation costs while ensuring timely stock replenishment are also some crucial activities in order fulfillment.
Why Does Intelligent Replenishment Matter?
Inventory replenishment or stock replenishment means restocking inventory in a warehouse such that the consumer demand is met optimally without overstock or out-of-stock events. While overstocking ties up the working capital, out-of-stock instances directly impact sales and customer experience.
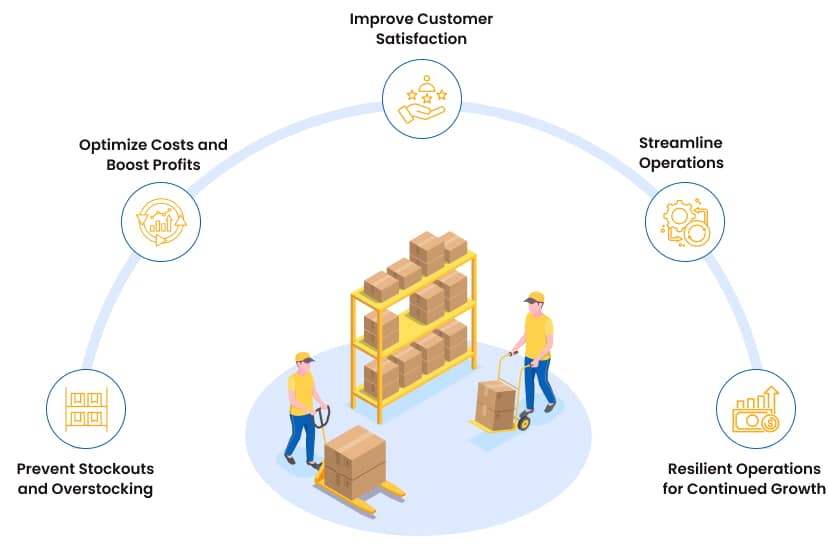

Prevent Stockouts and Overstocking
While stockouts lead to frustrated customers and lost sales due to required items not being available, overstocks can damage a business by having them in plenty, more than what is required to cater to customer demand.
Overstocking can tie up valuable capital in underutilized inventory, leading to potential write-offs, and increased costs from prolonged storage, product expiration, trends, etc. Efficient replenishment planning strikes a balance between both. By accurately forecasting demand and optimizing order quantities, businesses can easily have the right inventory levels, minimize stockouts & overstocking, and unlock greater cost savings.

Optimize Costs and Boost Profits
Poor replenishment can bloat inventory levels, thereby incurring higher costs for storage, premiums, and the risk of obsolescence. On the other hand, optimal replenishment can slash inventory holding costs via intelligent replenishment insights built on accurate forecasting.
Businesses can order only what they need, when they need it, and can easily crank the quantities up and down based on demand trends, and sudden spikes or lows. This frees up capital for other business investments and improves profit margins.
They can tactically avoid scenarios such as overstocks and stockouts while catering to customer demand in an optimal manner, which also reduces the costs across the entire value chain, thereby strengthening the bottom lines further.

Improve Customer Satisfaction
Accurate replenishment planning reduces stockouts and ensures higher shelf availability, which elevates overall customer satisfaction. As the customers are able to get what they want as and when required, the entire shopping experience becomes delightful, increasing customer loyalty as well.
This also translates into repeat business, sustained growth, and a healthier bottom line. On the other hand, poor replenishment planning can seriously damage the customer experience with events like stockouts and bottom lines due to overstocks.

Streamline Operations
Replenishment planning is a systematic approach to inventory management and goes beyond ordering inventory. Hence, it helps to streamline various business operations across the entire value chain – from sourcing to ordering and planning for order fluctuations to ensuring the right stock levels.
Automating reorder points and optimizing delivery schedules also frees up valuable man-hours and improves operational efficiency. Furthermore, having the right data at hand through proper replenishment practices facilitates better decision-making, making supply chains smoother and more efficient.

Resilient Operations for Continued Growth
Effective replenishment planning helps businesses dynamically adjust to demand fluctuations, near-future supply chain disruptions, and demand patterns for long-term and short-term strategies. They can leverage accurate forecasting to put contingency plans in place and adapt to changing circumstances in a flexible manner.
Overstocking can tie up valuable capital in underutilized inventory, leading to potential write-offs, and increased costs from prolonged storage, product expiration, trends, etc. Efficient replenishment planning strikes a balance between both. By accurately forecasting demand and optimizing order quantities, businesses can easily have the right inventory levels, minimize stockouts & overstocking, and unlock greater cost savings.
Case Study
What Impacts Inventory Replenishment: External & Internal Factors
Inventory replenishment or stock replenishment means restocking inventory in a warehouse such that the consumer demand is met optimally without overstock or out-of-stock events. While overstocking ties up the working capital, out-of-stock instances directly impact sales and customer experience.
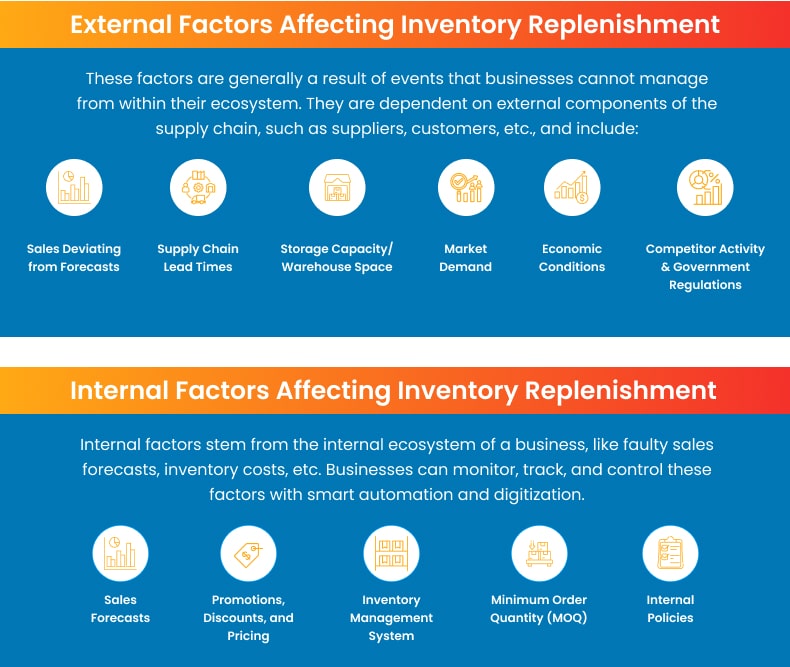
Optimizing Inventory Replenishment
Optimized inventory ensures the right amount of inventory, in the right place, at the right time, and is built upon intelligent replenishment strategies powered by automation.
Static replenishment planning relies on manual data handling and random adjustments for holidays and promotions that are based on hunches, instead of reliable data. This leads to cost bleeds owing to overstocks, out-of-stocks, cannibalization, and more. Further, the data in retail is generally fuzzy, sparse, and noisy, which makes it highly unsuitable for parsing via traditional methodologies.
On the other hand, automation-powered replenishment solutions utilize AI and ML to overcome data hurdles and generate hyper-accurate forecasts at hyperlocal levels. This means they can optimize inventory in a granular manner based on product location nuances, and fluctuations in demand to boost sales and make the most of promotional events without succumbing to cannibalization.
Apart from saving businesses from high inventory investments, automation-driven replenishment also minimizes unnecessary losses due to spoilage.
With consistent product availability, businesses can unlock greater levels of customer satisfaction which paves the way for customer loyalty. Automated inventory planning also frees up valuable time and resources.
Benefits of Replenishment Optimization

Better Availability & Higher Customer Satisfaction
Optimal inventory means customers find the desired products on shelves when they need them irrespective of the seasonal highs and lows. This translates into reduced stockouts and overstocks, happier customers, stronger market standing, and improved brand loyalty.

Improved Profitability
Accurate forecasting generates reliable and data-driven replenishment decisions, which means businesses have balanced inventory levels at all times. They are no longer adjusting the order values to random hunches and are fulfilling customer demands via strategic stocking.
This improves profit margins by allowing businesses to maximize sell-through rates while safekeeping investment from excess stocks

ROI Reinvestment Opportunities
Recent studies reveal that 57% of organizations globally are planning to increase investment to make their supply chain resilient, while 66% of them are focusing their investments on reducing supply chain costs.
Data-driven replenishment planning creates more working capital and boosts profitability across the entire value chain. This creates a lucrative opportunity for all the supply chain stakeholders in terms of reinvestment in future growth initiatives, from digitization to network expansion, and more.

Reduced Waste
Replenishment optimization stands on accurate forecasting, which identifies trends, seasonality, and demand patterns for multiple external and internal factors, down to the store level. This means businesses can easily eliminate wastage owing to spoilage, expiration, as well as obsolescence in an effective manner, thereby boosting the overall supply chain efficiency.

Enhanced Visibility
Capgemini reports that only 9% of organizations across the globe report visibility into the upstream and downstream supply chain network with particular emphasis on data-sharing capabilities.
Intelligent replenishment solutions come with an end-to-end automation framework with a highly intuitive and integrated dashboard. This not only helps demand planners and supply chain managers to gain visibility over key milestones, forecast models, and granular data but to adjust replenishment plans dynamically in real time based on custom triggers and alerts.
They can share highly reliable numbers with the relevant stakeholders as and when required and achieve operational efficiency at scale.

Reduced Operational Costs
As mentioned above, reducing operational costs is one of the top priorities for supply chain management stakeholders across the globe. AI and ML-powered replenishment optimization solutions offer intelligent insights that can steer businesses toward more balanced and strategic inventory management.
They can optimize their strategies at a highly granular level, so much so that every store has the right pack sizes, quantities, and bundles for all the products at all times. This level of optimization ensures cost-efficient operations, reducing inventory costs by as much as 10%.

Better Scalability
82% of consumer products and retail organizations have renewed their focus on shaping customer demand and creating cost efficiency across entire supply chains via better planning, automation, and process improvement. This is essential for sustainable scalability that doesn’t stand solely on hefty investment.
Optimizing inventory replenishment empowers businesses to adapt to network expansion, market, and supply-side disruptions, and demand fluctuations in an elastic manner.
But then again, where does one start when it comes to inventory optimization, and what are the common hurdles businesses face when it comes to optimizing replenishment in an intelligent manner?
Challenges in Inventory Optimization
Optimized inventory ensures the right amount of inventory, in the right place, at the right time, and is built upon intelligent replenishment strategies powered by automation.
1 Traditional/Legacy Systems
A whopping 84% of organizations are prioritizing improving crisis preparedness using simulation. This enables them to plan for business risks and continuity in a scenario-based manner, something they can never do with legacy systems.
Huge gaps in technology infrastructure, lack of interoperability, and high costs of integrations are some of the key implementation challenges. Further, the inability to generate accurate forecasts quickly and ensure agile adaptation to market and demand changes forms another world of problems.
2Data Quality Issues
A whopping 70-90% of stockouts are caused by poor stock replenishment. Further, as many as 84% of executives suffer from data silos, and as much as 40% of business-critical data is trapped in them.
Adding to the challenges is the inability to parse the highly unstructured and noisy data in an integrated manner to produce bankable insights. Traditional models for replenishment are neither capable of data analysis and modeling at a quick pace nor can they adapt to fluctuations without disrupting planning metrics, like cost, time, etc.
3Rapid Demand Shifts
Inaccurate demand forecasting can inflate inventory holding costs by up to 30%, eroding profit margins. While AI/ML-powered replenishment solutions can easily anticipate demand shifts owing to micro-trends for all product locations, traditional systems don’t have this ability.
Adding to the challenges is the inability to parse the highly unstructured and noisy data in an integrated manner to produce bankable insights. Traditional models for replenishment are neither capable of data analysis and modeling at a quick pace nor can they adapt to fluctuations without disrupting planning metrics, like cost, time, etc.
4Tricky Product Behavior
Not all products behave the same way, especially when it comes to challenging categories like meat, wine, etc. Some products exhibit seasonality and the demand fluctuates significantly across different seasons, like fresh food and beauty products.
On the other hand, some products might also exhibit variations in sales based on trends, such as influencer-led sales of specific types of lotion or shampoo. Likewise, some products exhibit huge surges or drops in sales based on life cycle stages, like certain health foods, which might demonstrate unpredictable initial demand, which slowly declines as the product matures.
Such behaviors make it challenging for businesses to accurately forecast demand and ensure optimal inventory levels at all times, without the support of technology.
5Data Quality Issues
As much as 67% of CXOs globally are prioritizing and increasing investments in disruption detection and innovation processes. This stems from the fact that modern supply chains are becoming increasingly complex and interconnected.
This means sudden disruptions, like delays in delivery owing to port congestions, poor visibility leading to detention and demurrage, and more, can occur at any point. Further, natural disasters, geopolitical events, and supplier issues can derail replenishment planning significantly.
Optimizing Inventory With Intelligent Automation
Optimized inventory ensures the right amount of inventory, in the right place, at the right time, and is built upon intelligent replenishment strategies powered by automation.

AI/ML-Based Forecasting
AI/ML-based forecasting has up to 97% forecast accuracy that can reduce out-of-stock events by a significant 90%, and inventory days by as much as 30%.
AI/ML-powered forecasting solutions can auto-generate thousands of unique forecasting models for each channel, category, and store combination. Businesses can set specific risk levels to ensure best-fit model selection based on category objectives.
They can predict demand shifts between similar products due to factors such as promotions and shelf availability, and elevate forecasting accuracy by incorporating key predictors tailored to each channel, store, and category

Seamless Collaboration Across Upstream and Downstream Trading Partners
Automation-powered intelligent demand forecasting and replenishment facilitates accurate inventory management by analyzing real-time data, frequently changing demand patterns, and market fluctuations. Improved collaboration in the supplier network directly influences as much as 20% of total revenue apart from other key metrics such as customer experience and cost of operations.
Sharing demand forecasting and replenishment data with suppliers enables them to meet the current business needs efficiently while boosting profitability for both parties and timely procurement of the right inventory. This collaboration not only helps suppliers plan production, fulfillment, and procurement, but it also fosters a strong and mutually beneficial relationship.

Advanced Data Processing and Analytics
Automated replenishment optimization solutions come with built-in data analytics capabilities that empower demand planners and key supply chain stakeholders in an organization to draw actionable insights from diverse modeling techniques.
They can select specific combinations of different modeling algorithms to arrive at highly accurate forecasts for inventory planning. They can further optimize their replenishment strategies for near-future demand fluctuations and custom triggers for predictive tuning.
Automation also facilitates supplier data analysis for strategic supplier selection, thereby unlocking greater value and fostering stronger partnerships. Businesses can check historical performance, individual scorecards, etc., to prioritize the most suitable suppliers.
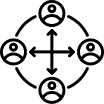
Cross-Departmental Planning
A lack of mutual trust and communication tops the list of challenges for 63% of retailers and 52% of suppliers. Further, delays in responding to inquiries can lead to a 20-30% increase in lead times, impacting overall supply chain efficiency.
Intelligent replenishment optimization solutions come with centralized collaboration and communication functionalities. Thus, users can create automated responses, offer resolution via multiple devices in real-time, and collaborate across multiple channels to ensure timely response, efficient communication, and seamless supplier collaboration.

Automated Replenishment and Inventory Management
Inventory replenishment solutions can effortlessly automate forecasting for daily, weekly, and monthly milestones with built-in effortless scheduling workflows. They can elevate forecasting accuracy by incorporating key predictors tailored to each channel, store, and category.
Demand planners and supply chain executives can easily Integrate internal elements such as promotions, historical sales, marketing spending, and external influences such as holidays, events, and temperature to generate highly optimal replenishment plans at all times for all levels.

Storage and Space Optimization Capabilities
Annually, $163 billion worth of inventory is discarded due to oversupply and damage. While traditional replenishment planning solutions fail to rise to the occasion, ML-based forecasting is highly accurate across all levels, categories, locations, SKUs, etc.
Thus, businesses can easily eliminate over-ordering, minimize storage costs, and reduce the risk of expired products. This further improves the overall operational efficiency and makes planning more resource-efficient.

Cannibalization Management
AI/ML-powered solutions can effectively handle in-store product cannibalization by dynamically balancing demand between products, and considering promotions and product availability.
Thus, businesses can automatically adjust replenishment levels up or down to align with the shifting demand. Further, they can automatically optimize inventory across the supply chain by supporting direct store orders, warehouse-to-store orders as well as warehouse orders.
Intelligent Inventory Optimization Strategies to Reduce Costs and Improve CX
By now, it must be clear that optimizing replenishment to reduce costs while boosting customer experience is a process that depends on multiple variables. Hence, strategizing requires multiple excellent capabilities supported by cutting-edge technologies. Next, we discuss how businesses can strategically optimize their inventory.
Choosing the right software platform is the foundation of successful inventory optimization. Right from comprehensive functionalities delivered via an integrated user interface to scalability and seamless integration capabilities – intelligent replenishment solutions can skyrocket forecast accuracy and demand planning.
Some of the key considerations for creating optimal replenishment plans are as follows
- Consolidate data across all functions and components for gaining actionable insights and informed decision-making.
- AI and ML-based forecasting to enhance forecasting accuracy and streamline planning across merchandising, supply chain, and operations.
- Factor in external influences such as promotions, competitor activity, and economic trends for a more comprehensive demand modeling.
- Go beyond regional trends and forecast demand at a granular, store-by-store, and product-level, also called product-location level for targeted inventory allocation.
- Plan for supply chain disruptions such as delays, etc., that can impact the inventory to ensure proper stocks at all times.
- Avoid unnecessary inventory build-up by intelligent optimization of reorder points and order quantities.
- Respond to demand fluctuations in an elastic manner for unexpected demand surges to prevent stockouts and maximize customer satisfaction.
Such pin-point strategizing requires data-driven planning stemming from strong technical and automation infrastructure, which is scalable, agile, and responsive. This is where Algonomy’s Order Right steps in.
How Can Algonomy Help?
Algonomy’s Order Right is an AI/ML-powered intelligent replenishment platform that comes with built-in forecasting running on cutting-edge technology infrastructure. With an ensemble algorithmic approach, custom fine-tuning of forecasting algorithms for specific business nuances, and built-in capabilities to mitigate supply chain disruptions without causing inventory chaos, Order Right paves the way toward effortless and intelligent replenishment
The solution can generate accurate SKU-level order plans for even the most challenging categories with AI-powered replenishment planning, thereby enabling retailers to overcome data parsing challenges like noisy and sparse data
Order Right can effectively handle in-store product cannibalization by dynamically balancing demand between products, considering promotions and availability.
Further, it empowers businesses to ensure optimal inventory even during supply chain disruptions using adaptive self-learning models that optimize replenishment plans by factoring in lead time, MOQ, minimum size pack, safety stock, display minimums, and pending orders
We help businesses across diverse industries unlock as much as 97% forecast accuracy with proprietary AI-driven custom feature engineering and model selection for demand forecasting.
Further, businesses can easily mitigate future inventory headaches and maximize efficiency with predictive alerts for days of stock situations, excess stock, and expiring products, take corrective action proactively, and unlock:
- 10% Reduction in Inventory Costs
- 75% Reduction in Out-of-Stocks
- 10-30% Reduction in Wastage
- 99% Increase in Shelf Availability
To know more, or to catch Algonomy’s Order Right in action, please get in touch with our experts and schedule a free demo today!